WORK SCENERY作業風景
設計DESIGN
工場等の自動化や生産効率アップなど、お客様のご要望をヒアリングした上で、必要な装置を計画し、図面を作成する仕事です。製品の製造機械でも、検査機でも、装置に求められる生産能力やスピード、機械のサイズ、製作コストなど、クリアしなければならない要素は様々です。CADを使用して大まかな構想図を作成・提案し、打ち合わせを重ねながら目的する装置となるまで設計・図面化を繰り返します。とても多角的な視点を必要とする業務です。
展開DEVELOPED FIGURE
設計段階で作成された立体物図面の各部品を、CADを使用して平面図=展開図に置き換える仕事です。材料となる鉄板は、曲げることで寸法が伸縮するため、その伸び率も計算に入れて図面化していきます。平面化する中で、レーザー加工機で鉄板を切断できるようデータを作成します。また、機械で材料を無理なく曲げられるよう工夫することも重要です。最後にネスティングと呼ばれる、材料資源を有効活用するデータ配置を行い、切断工程に渡します。
切断・穴あけCUTTING / DRILLING
展開工程で作成されたデータを用い、レーザー加工機で鉄板を切断したり、穴をあけたりする仕事です。オペレーターは加工機への材料のセットや、機械の操作を行いますが、すでに一部使用済みの鉄板を再度使う場合、全自動での加工を行うことはできません。その場合は座標軸を手動でセットする等の操作を行います。1枚の大きな鉄板から効率よく部品を抜き、部品ごとに仕分け作業を行っていきます。また、レーザー加工機ではあけられないような小さな穴が必要な場合は、ドリルを使って手作業であける場合もあります。
板金〈曲げ〉SHEET METAL bending
ベンダーと金型を用いて、部品ごとの曲げ加工を行う仕事です。ネットワークを通じて展開工程から送信されたデータを使用し、機械に部品をセットすることで加工が可能となる自動機と、曲げの度合いを自在にコントロールできる手動機があります。V字型の溝のある金型に部品を押し当て、溝の方向に材料を変形させる形で曲げていきます。しかし場合によっては全自動では曲げられないケースもあります。その場合経験とノウハウを活かし、セオリー通りではない金型を用いるなど創意工夫によって目的の形状となるよう加工を行っていきます。
板金〈溶接〉WELDING SHEET METAL
金属材料を溶かし、部品同士を結合させていく溶接の仕事です。ヤマモトでは3種類の溶接機を使い分けており、それぞれ半自動溶接機、ティグ溶接機、ファイバーレーザー溶接機と呼ばれています。半自動溶接機は溶接棒と呼ばれる材料を別途準備し、それを溶かしながら部品に盛っていくことで接合します。ティグ溶接は、材料と電極棒の間に電流をスパークさせ、材料を溶かすことで接合させます。ファイバーレーザーはレーザー光線を当てることで材料を溶かして接合します。特に半自動溶接とティグ溶接は、製品に歪みが出てしまうこともあるため、歪みを計算した上で角度をつけながら溶接するなどの工夫が必要になります。
塗装PAINTING
溶接工程を経て出来上がった製品に色を塗る仕事です。ヤマモトは形状やサイズなどが様々な製品を塗装しているため、すべてエアガンを用いた手塗り作業を行っています。この工程では、まず脱脂作業と呼ばれる製品の油分を取り除く作業を行います。その後、製品ごとに指定された色に塗っていくことになりますが、季節や日によって湿度や気温が異なるため、塗料の配合を微妙に変化させる必要があります。下塗り、上塗りと色を重ねていったあと、ガス炉に入れて120℃の温度で焼付を行います。これによって、接触しても塗料がはがれない状態に仕上がります。多くの製品は塗るべき塗料が決まっていますが、場合によっては塗料を混ぜて調色を行う場合もあります。
組立・調整ASSEMBLY
機械製品に必要な部品を集め、図面に基づいて機械を組み立てていく仕事です。プラモデルの延長のようなイメージではありますが、ヤマモトは製品の製造に使う機械や検査に使う機械など、実用性が求められる機械を製造するため、組み立ての「精度」によって結果が大きく変わります。例えば、完全にまっすぐ取り付けられているべき部品が斜めにつけられている場合などは、機械の動きに負担がかかり、モーター等にも負荷がかかります。つまりこれが故障の原因となります。このため、0.05mmの精度で丁寧に調整をしていきます。また電気配線もこの部署で行い、機械に信号を送るための電気配線、制御盤の製作なども行っていきます。
工場FACTORY
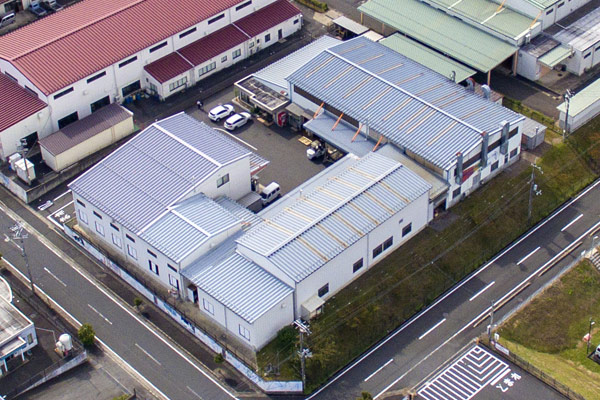
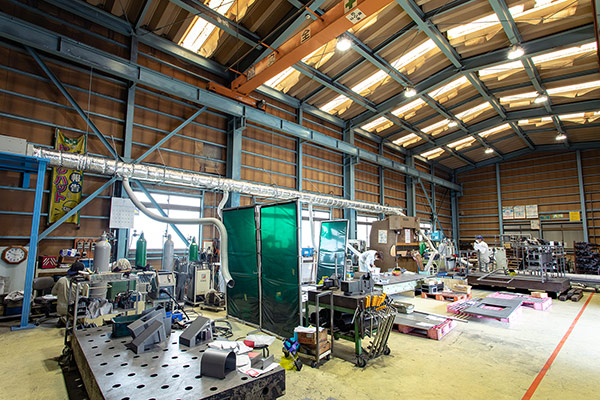
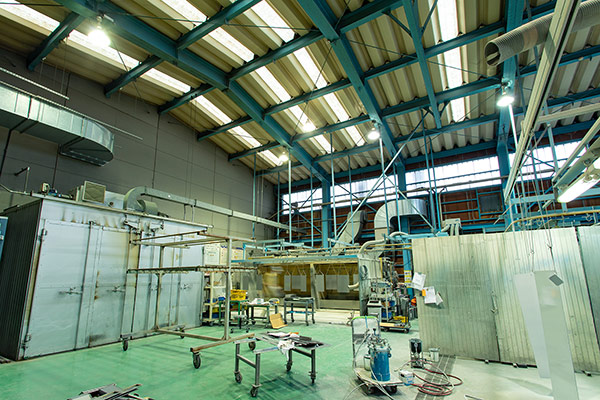
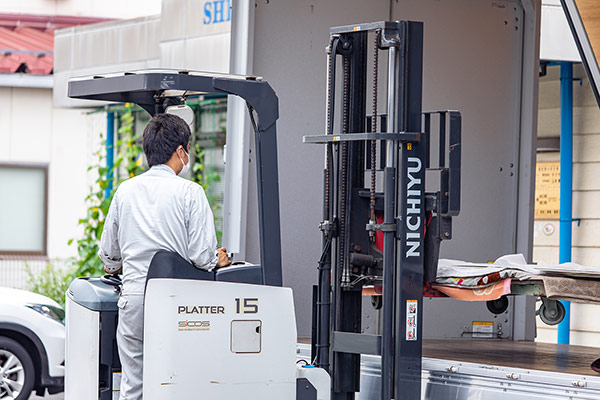